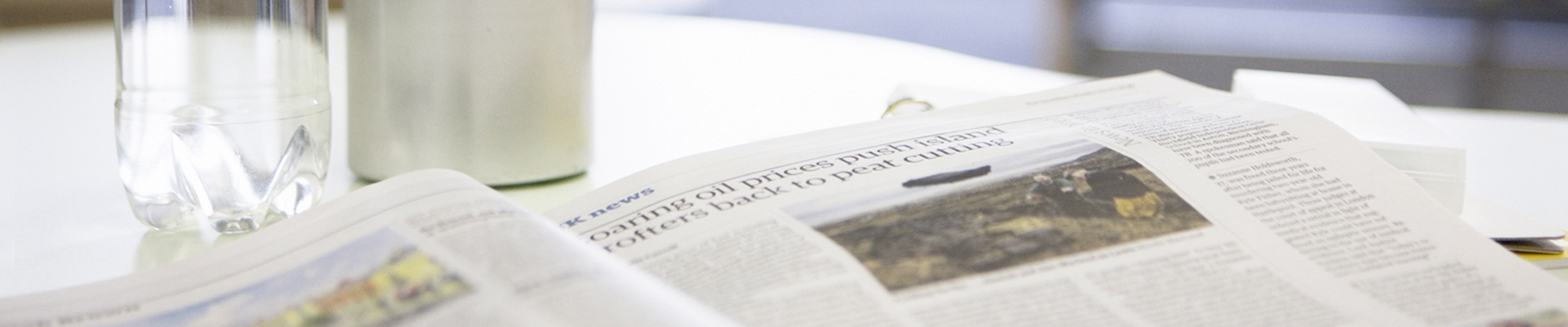
生物制药行业废气治理解决方案
生物制药行业废气治理解决方案
现状分析
随着制药行业的发展,随之而来的环境污染问题日益凸显,特别是制药行业有机废气的区域环境污染,严重影响居民的正常生活。跟据环保部之前公布的数据显示,中国制药工业总产值约占全国GDP的比例不到3%,而污染排放总量却占到了6%左右,其中高污染、高能耗的原料药行业问题尤为突出。
在制药行业中大量使用有机溶剂(如DMF、苯系物、有机胺、乙酸乙酯、二氯甲烷、丙酮、甲醇、乙醇、丁酮、乙醚、二氯乙烷、醋酸、氯仿等),挥发形成了具有刺激性气味和恶臭的气体,并具有一定毒害性,长期排放必然恶化区域大气环境质量,并对附近居民的身体产生危害。因此,有效治制药行业VOCs污染已经成为亟待解决的重要问题。
废气来源
在生产过程中,制药企业会使用到一些溶点低、挥发性好的有机溶剂。此类溶剂很可能会随着生产过程挥发出来而导致VOCs污染,VOCs排放主要发生在投料、反应、溶剂回收、过滤、离心、烘干、出料等操作单元。
废气特性
溶剂废气排放特点主要跟医药化工生产工艺特点有关,具体表现在:
1)排放点多,排放量大,无组织排放严重。因其溶剂消耗大,且具有挥发性。几乎每台生产设备都是溶剂废气排放点。溶剂废气大多低空无组织排放, 厂界溶剂废气浓度较高;
2)间歇性排放多。反应过程基本上为间歇反应, 溶剂废气也呈间歇性排放;
3)溶剂废气成分复杂,污染物种类和浓度变化大,同一套装置在不同时期可能排放不同性质的污染物;
4)溶剂废气影响范围广。溶剂废气中的VOCs大多具有恶臭性质,嗅域值低,易扩散,影响范围广;
5)“跑冒滴漏”等事故排放多。由于生产过程中易燃、易爆物质多,反应过程激烈,生产事故风险大,加上生产装备水平和工艺技术水平较低及管理不善,造成“跑冒滴漏”等事故排放多。
设计依据
根据国家及行业相关标准和规范,为客户提供定制化的治理技术方案,主要涉及依据如下:
《中华人民共和国环境保护法》;
《中华人民共和国大气污染防治法》;
《大气污染物综合排放标准》 GB16297-1996;
《恶臭污染物排放标准》 GB 14554-93;
《吸附法工业有机废气治理工程技术规范》 HJ2026-2013;
《催化燃烧法工业有机废气治理工程技术规范 》 HJ2027-2013;
《工业企业噪声测量规范》GBJ122-88;
《工业与民用供配电系统设计规范》GB50052-2009;
《通风与空调工程施工质量验收规范》GB 50243-2002;
河北省地方标准DB13/2208-2015《青霉素类制药挥发性有机物和恶臭特征污染物排放标准》;
河北省地方标准DB13/2208-2015《青霉素类制药挥发性有机物和恶臭特征污染物排放标准》;
上海市地方标准DB31/373-2010《生物制药行业污染物排放标准》;
浙江省地方标准DB33/923-2014《生物制药工业污染物排放标准》;
选择有机废气处理方法,需要根据以下因素:有机污染物质的类型、浓度水平、排气温度、排放流量、微粒散发的水平、需要达到的污染物控制水平等。有机废气的处理方法种类繁多各有优劣。常用的有冷凝法、吸收法、燃烧法、催化法、吸附法、低温等离子、生物法、光催化氧化法、蓄热式氧化法等。
治理方案
1)针对某些制药行业有机废气尾气中风量大、浓度中低或者浓度不稳定、成分复杂及难以回收利用的场合下,建议采用活性碳颗粒对有机物进行高效吸附。
2)针对某些制药行业有机废气尾气中风量小、浓度高、成分复杂及难以回收利用的场合下,建议采用高效能蓄热式燃烧装置(RTO)处理后排放。
3)针对某些制药行业有机废气尾气中风量小、浓度高、成分复杂及难以回收利用,不含氯磷等易使催化剂中毒的元素的场合下,建议采用活性炭吸附脱附+催化燃烧装置处理后排放。
1)活性炭吸附技术方案
方案概述
针对某些制药行业有机废气尾气中风量大、浓度中低或者浓度不稳定、成分复杂及难以回收利用的场合下,建议采用活性碳颗粒对有机物进行高效吸附,净化废气中的有机成分,然后采用水蒸气脱附回收废气中有价值的成分,最终达到环保要求和资源回收的目的。
工艺流程
活性炭颗粒吸附回收有机废气装置设置多个吸附器,共用一套管路系统,运行时吸附器依次进入吸附状态。有机废气经预处理后由吸附器下部进入吸附器内部,穿过活性炭,净化后的气体由吸附器顶部排出。
工艺流程图:
2)蓄热式燃烧装置(RTO)技术方案
方案概述
针对某些制药行业有机废气尾气中风量小、浓度高、成分复杂及难以回收利用的场合下,建议采用高效能蓄热式燃烧装置(RTO)处理后排放。系统采用两室、三室或多室RTO,处理效率可达95-99%以上,同时能充分收集有机废气燃烧产生的热能,用于装置运行。
制药车间经预处理的废气先首先经过蓄热室预热,然后进入燃烧室,加热升温到800℃左右,使VOCs氧化分解成CO2和H2O;氧化后生成的高温烟气再通过另一个蓄热室释放热量,然后排出RTO系统。三室型RTO运行操作过程,单个蓄热室在进气、吹扫、排气三种状态之间反复切换,当一个循环后,VOCs始终进入到在上一循环时排出净化气的蓄热室,而原来进入VOCs的蓄热室则用净化气或空气清扫,并将残留的未反应VOCs送回至燃烧室进行氧化,然后与净化气一起从冲洗过的蓄热室排出。 该过程不断循环交替,从而有效降低废气处理后的热量排放,同时节约了废气氧化升温时的热量损耗,使废气在高温氧化过程中保持着较高的热效率(热效率95%左右),其设备安全可靠、操作简单、维护方便,运行费用低,VOCs净化效率高达99%。
工艺流程:
3)活性炭吸附脱附+催化燃烧装置技术方案
方案概述
活性炭吸附浓缩+催化氧化组合工艺适用于低浓度不宜采用直接燃烧或催化燃烧法及不须吸附浓缩回收处理的有机废气,尤其对大风量的处理场合,可获得满意的处理效果。与回收类有机废气净化装置相比,无须备压缩空气和蒸气等附加能源,也无须配备冷却塔等附加设备,运行过程不产生二次污染,设备投资及运行费用低。,实现了整个系统的净化、脱附过程密闭循环。
工艺流程
有机废气先通过干式过滤,将废气中颗粒状污染物截留去除,然后进入活性炭吸附床进行吸附,利用具有大比表面积的蜂窝状活性炭将有机溶剂吸附在活性炭表面,处理后干净的气流经过风机、烟囱高空排放。
活性炭经过吸附运行一段时间后达到饱和,启动系统的脱附-催化燃烧过程,通过热气流将原来已经吸附在活性炭表面的有机溶剂脱附出来,并经过催化燃烧反应转化生成CO2和水蒸气等无害物质,并放出热量,反应产生的热量经过热交换部分回用到脱附加热气流中,当脱附达到一定程度时放热跟脱附加热达到平衡,系统在不外加热量的情况下完成脱附再生过程,即吸附过程为连续式处理工艺,在备用吸附装置投入使用同时,饱和吸附箱则进行脱附工作,脱附后活性炭箱预备至下次循环使用。
工艺流程:
以上方案为制药行业常规解决方案,针对不同企业有不同的工况及解决需求,我公司可根据用户要求进行方案设计,出具科学合理的除尘及废气解决方案。随着用户要求越来越高,还有生态环境部的要求,现在一般采用多级治理技术的方式,那么如何选择最经济合理、治理效果最好的多级治理方案显得尤为重要。详情联系15564537088.